‘It-Trab’
The screaming noise of a blade going through stone followed by a white cloud of dust:
This is a sight one expects to see on any construction site regardless of the size of the project. One wouldn’t believe anyone who claims to be a builder if the person wasn’t covered in white dust arising out of the Maltese Limestone. Why is everyone complacent to the dust generated by such works? Should be people be concerned?
Limestone is naturally occurring and contain varies amounts of quartz (crystalline silica). This mineral is not dangerous in its bulk form and is safe to use. However, when the material is processed, cut or broken down it may create dust which contains respirable crystalline silica. As such, any quarry, mining and most building activities involve crystalline silica (https://www.eula.eu/crystalline-silica/).
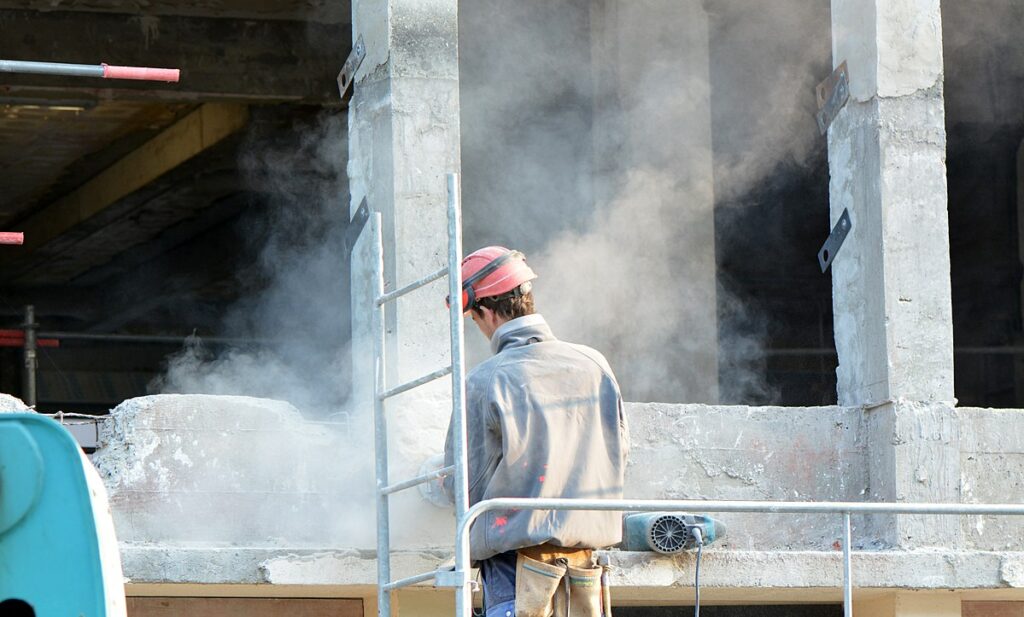
If inhaled, respirable crystalline silica may settle in the lungs which is then attacked by the immune system. This may cause swelling which may lead to scarred tissue (fibrosis). As a result, a person may develop a persistent cough, shortness of breath and a feeling of tiredness. These are the symptoms of silicosis which also increases the risk of a person getting other serious conditions such as chest infections, lung cancer and arthritis Silicosis – NHS (www.nhs.uk).
Respirable crystalline silica is regulated in Malta by S.L.424.35 Protection of Workers from the Risks related to Exposure to Carcinogens or Mutagens at Work Regulations . Amongst others the employer has a duty to carry out the following; assessments, reduction of exposure, implementation of technical measures and making arrangements for health surveillance.
The law is quite technical and somewhat difficult to interpret. However, if we look at guidelines issued by the Health and Safety Executive (HSE) we better understand what is required to protect oneself from silica exposure.
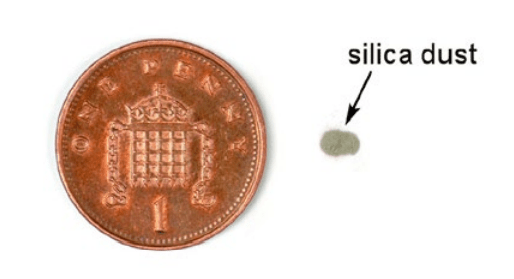
To put us in perspective of how important the following measures are, the HSE published this image which shows the amount of inhaled silica, not be exceeded per day.
In certain circumstances, dust can be avoided altogether by purchasing the correct size of material or using direct fastening systems. Having said that, the generation of dust may be inevitable, as such tool extraction and respiratory protective equipment is to be used to reduce and protect against exposure to dust (Construction dust CIS36 (hse.gov.uk)). In Malta we sometimes see construction site workers using water damping devices however this is not a common sight to see.
Dust exposure is so serious that the HSE has been running a campaign called ‘Dust Buster’ whereby HSE inspectors check on construction sites to ensure that the above controls are implemented and that workers are aware of the risks involved (“Health and Safety Executive cracks down on dust – HSE Media Centre”, 2020).
In 2001 there were 485 cases of silicosis in the European Union (Karjalainen & Niederlaender, 2004). These exclude other respiratory problems which arise out of dust and have not been diagnosed a Silicosis. Such as, lung cancer, chronic obstructive pulmonary disease (COPD) and asthma.
So how come we still expect builders to be covered in dust? How come dust bothering neighbours of construction sites, is still considered a nuisance and nothing else? How come workers still refuse to wear appropriate PPE? Aren’t we all tired of seeing dust-covered cars, dust-covered roads, dust-covered buildings and dust-covered people?